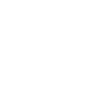
Pricing
Bench rate: $99/hour
Free Evaluation and Estimates
Free Labour for Kids/Students <18
Full Setup: :
Guitar or Bass (Electric or Acoustic
Evaluation | $0 |
Full Setup (You get a LOT of extras in my setup compared to retail places) | $120 |
Requires neck removal for truss rod adjustment | Add $10 |
String cost not included, but I have a huge inventory…no markup on prices |
A Set-Up (it’s not a “Tune-Up,” because it’s not a lawnmower or a prostate) begins with a free overall evaluation of the instrument (structural, hardware, electronics) and a “health check” (like a prostate) of the 3 major geometrical measurements (relief, action/neck angle, nut height). Any issues will be discussed (not prostates), and a work estimate given. A standard Full Setup takes 75 minutes, and includes : truss rod adjustment, fret “rocking” (checking for high spots), minor fret spot-filing (3 for free, surcharge for more), all frets crowned and polished, fretboard hydration, guitar nut (evaluation, material, condition, height, precision nut slotting and string protrusion), hardware lubrication/torque, electronics (corroded potentiometers, intermittent jacks), restringing (your choice of strings, but I might suggest), action/playability customized to YOUR style, (including tremolo systems), final intonation, pickup height and balance (relative output), naphtha body cleaning, hand-polished or or Stew-Mac buffing arbor final polish. Then, you come and play it, and we make tweaks and adjustments. When you’re happy, I’m happy, and you pay me, and I spend it all on our dumb horses.
Bridge and Saddle Replacement Electric and Acoustic Guitar and Bass
The bridge is the wooden part on an acoustic where the pins go in. The saddle is the long bone/TUSQ/Plastic (ugh) piece that contacts the strings, and the profile and height are critical to string action/feel. On an electric, the bridge is usually metal, rests on the guitar body, and the saddles contact the strings. Upgrading an old or cheapie electric bridge transforms a guitar. You’ll get wonderful intonation, string spacing, string radius, smooth adjustability, not to mention tonal bliss. Almost every acoustic guitar needs saddle lowering/shaping/sanding or replacement, and you need the right saddle material for the guitar. Did you know that beautiful, expensive organic bone saddles don’t always work with certain pickup systems? I do. Or that the bottom profile of a saddle shouldn’t always be square. What? I see a LOT of well-intentioned DIY jobs on saddles that are killing the action, tone and break angle of strings. Please enjoy the video below, complete with subtitles.
Electric: Saddles / Bridge Guitar or Bass | Whatever the saddle costs + setup |
Acoustic: Saddles / Bridge Guitar or Bass | $30 TUSQ, $50 (and up) bone. (setup usually required) |
Fretwork
Fretwork is the bread and butter of a good repair shop. Big stores charge $350 for a PLEK (CNC laser job) and setup (and months of wait time), or $300 for a hand-job (what?) and YOU supply the strings. Ouch.
It takes expensive tools, time and a LOT of experience to do correctly, removing just a whisper of material. Nearly every guitar, new or old, has some form of fretwork to be done. Minor spot-leveling is included in my Full Setup package. Usually, that’s 2 or 3 outlier high spots that need to be tamed and crowned. Beyond that, we’re into more complex fretwork. High frets are identified by using a Fret Rocker, and sharpie run along the offending areas. Then, I’ll either file with a 3-corner dressing file, or if it’s really wonky in several places (like loose teeth on a redneck), I use radiused blocks with 400 grit 3M Gold stickit paper and remove only the bare minimum of material. Once the fret tops are even and radiused, I crown and do a 9 step hand polish using Micro-Mesh 1200 to 12000 grit pads. BLING! Smoother than my dance moves. Like, way smoother. For ouchy frets ends (worse in the wintertime…I do a lot of them January-March), you need a fret edge dress. It’s a long process, because I use a tiny diamond-grit file, not a horrible sanding block. Pro Tip: don’t use spring-loaded capos. The excessive clamping force can leave deep divots in frets 1 to 5, typically the plain B and high E strings.
Fret Edge Dress (Sharp Frets) | $50 |
Level, Crown and Polish | $15/fret (first 3 are covered in the Setup package) |
Nut Replacement
Insert Nut joke here. I’ll wait. Done? You sure? So immature.
Okay, I’m throwing the gauntlet here. 90% of guitars have improper nut values. Yes, I’m talking to YOU, Dear Reader. Even brand new $$$ name-brand ones. Slap a capo on a $4,000 guitar in a showroom, and enjoy the sharp intonation and need to re-tune. How dare they? Don’t they know who I AM, and what I PAID? Yes, they do.
Here goes: Guitars are shipped worldwide, and have to have generous (high) nut and saddle values to account for local humidity and temperature conditions. It’s like the driver’s seat button in your car; it’s there, but you have to adjust it to your anatomy after the 6’7″ mechanic hops out. This makes a huge difference in playability, tuning stability, tone, intonation up the neck, string-binding, allowing strings to ring freely, and eliminating annoying open-string buzz. Minor nut slotting (for string height and free movement) is included in the Setup package, but a full nut replacement is all about precision tools and experience. It’s very easy to “ruin” a nut setup. Premade TUSQ nuts are not “drop-in” solutions: they are model-specific with pre-shaped top profiles, but are purposely oversized, and have to be filed, sanded, slotted and mated. I’ll typically wear out a set of strings (hopefully, your old ones), because I have to tune up and down a dozen times to measure everything under tension, remove it, sand/file/slot/curse, tune up, replace the snapped G string…you get the picture. I have a large inventory of nuts and saddles, TUSQ and bone. BTW, music stores usually offer a “free setup” on new instruments, so you can start there. The results are adorable. You’ll be calling me soon afterward ; )
Tusq (self-lubricating) | $50 (setup usually required) |
Bone (bring your own lube) | $90 (setup usually required) |
Electronics
Repair – Replacements – Upgrades – Pick-Ups – Endpin Jacks – Pots – Noise Shielding
Ah, wiring. The elusive buzz. The intermittent crackling ground wire. Dirty pots. The 60-cycle hum at your mother-in-law’s, but not at home. Upgrade that Korean Epiphone to American Gibson parts. The desire to put P-90’s in a Hannah Montana 3/4 scale Costco guitar with a Floyd Rose and push-pull pots. Hell ya! Let’s do it!
PLEASE let me do the measuring and ordering of your parts. Half of my poor customers spend big bucks on fancy parts that simply don’t fit, and end up wasting money. Quality American parts on import guitars are amazing, but they often require drilling or Dremel work on the guitar to go from metric to American Imperial fitment. I don’t charge markup on parts, so you pay what I pay. I love hot-rodding, soldering, weird wiring schematics, toggle switches, push/pull craziness, upgrading cheap parts to premium ones and chasing down grounding issues. Nothing is “standard” in guitar-world fitment, so my experience will save you time and money over trying to DIY. Electronic Work: $99/hour, plus necessary parts (no markup)
Acoustic Pickup Systems
Baggs Anthem – K and K – Fishman – Budget Pickups – Piezo – Soundhole – Microphone
This is one of those “call me” scenarios. Do you want a pristine, microphone-quality sound for small cafés, or are you touring with Chicago surrounded by percussion and trumpets? First, we’ll choose a system ($25 to $500). Then, am I replacing an existing unit or do I need to drill end jack/bridge slot holes on a 1937 Martin? Le price, she will vary, là. Ballpark: an acoustic that has never had a pickup system: $75 for a decent system and $45 to 100 in labour (end-pin drilling, jack install, bridge drilling, saddle shaving, securing wires, battery mount, calibration.) The work is about the same, regardless of how expensive the system is.
Acoustic Pickup Installation | $40-100, depending on pickup type and complexity. Some types require a setup or saddle shaving afterward. |
Requires Consultation…There are so many options |
Structural Repairs
All structural repairs are billed at the bench rate of $99 per hour. Guitars are like onions…they can be straightforward, or multiple layers of awful that make you cry. For example, a lifting bridge or huge bellying on an acoustic may be symptomatic of popped/cracked braces underneath. So, now we have to glue/clamp/replace the brace(s) before tackling the removal/cleanup and re-gluing of the bridge itself. Onions…so many layers, and each layer is time and more tears.
Brace Repair | $65 and up |
Crack Repair | $65 and up |
Bridge Repair / Re-glue (epoxy= no-go. Throw in a raging river) | Dependent on complexity (budget 2 hours, I’ll advise you) |
Neck Shim on Electric | $40 + minor setup |
Neck reset on Acoustic The finer the quality ($$$) the guitar, the more likely a neck reset will be in your future. It could be 10, 20 years or more, but it’s likely. It’s the price to pay for a lightly-braced, resonant instrument under many foot pounds of torque (188 with medium gauge, or 162 with light gauge) for a sustained period of time. The neck block gets compressed, and you have wildly high action. If you are the original owner of a Martin/Gibson, or other fancy box, you may qualify for the lifetime warranty. I can look it over and advise. It could save you $600 plus. Taylors are easy and relatively inexpensive to do. Cheap guitars are more like robust furniture than musical instruments, and tend to be overbuilt. They sound like sofas, too.
|
*Bolt on, glued fretboard extension, graduated shim: $120 + setup. Normans and Seagulls, pre-2006 are typical. This is the budget option. *Bolt-on, glued extension, chisel-job: $450 + setup. Big job. *Traditional Dovetail reset $600 + setup. Huge job. *Taylor NT shim reset: $50, add cost of shims (there are 2) *Epoxied necks/bridges: Nope. Throw it in the nearest river, preferably raging. Or allow me to do it. Whee! Lots of newer Takamines (esp. G-series), post-2006 Seagull/Norman/Art and Lutherie/Simon and Patrick are disposable because they use epoxy in neck joints to save $20 during assembly. Boo!
|

Contact
Send a Message
Visit Us
Saint-Lazare, QC, Canada J7T2M7
Address will be shared upon appointment booking
No drop-ins, please. Bang-bang.
Text or Call
Open Hours
Monday – Friday: Evening drop-offs/pickups
Saturday – Sunday: 9 am – 8 pm